معاون خرید فولاد مبارکه:
خریدهای خطرپذیر باعث شده چرخه تکنولوژی در فولاد مبارکه با سرعت بیشتری حرکت کند
در یکی دیگر از برنامههای رادیوفولاد، مصطفی عطایی پور، معاون خرید فولاد مبارکه به تشریح اقدامات این واحد پرداخت. مشروح این گفتوگو را در ادامه میخوانید.
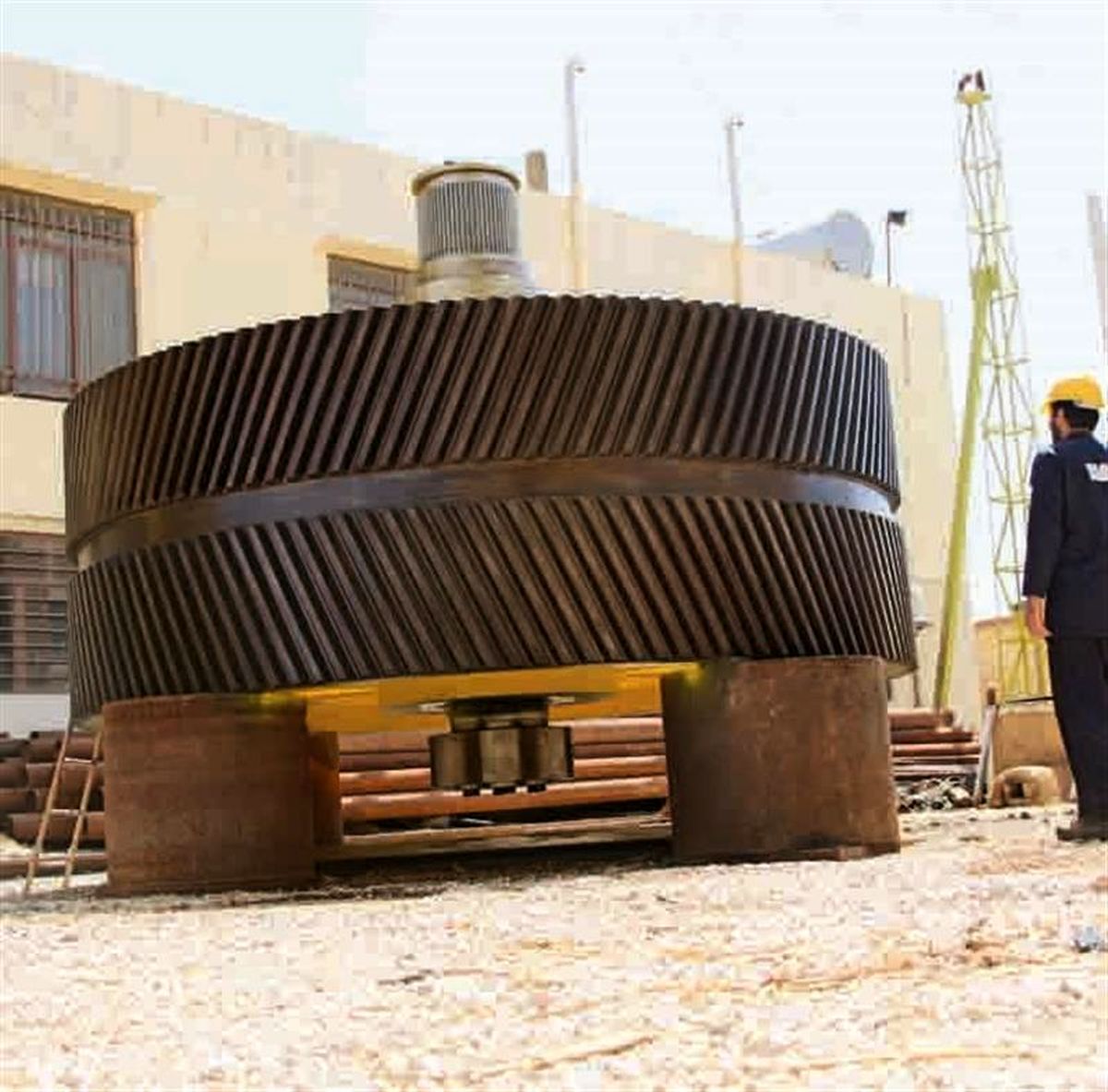
بهعنوان نخستین سؤال، ارزیابی شما از نقشآفرینی واحدهای زیرمجموعه معاونت خرید در ایجاد صرفههای اقتصادی برای فولاد مبارکه چیست؟
امروزه یکی از واحدهایی که میتواند برای شرکت کاهش هزینهها به ارمغان آورد و بهنوعی بخشی از سود را به شرکت بازگرداند واحد خرید است. خرید بر سه اصل استوار است و اگر این سه اصل بهخوبی انجام شود ما میتوانیم شاهد کاهش هزینهها باشیم.
یکی از این اصول کیفیت است. وقتی کالا یا قطعات باکیفیتی داشته باشیم، حتماً تعداد دفعات خرید کاهش مییابد؛ مثلاً در قطعات یدکی ممکن است تعداد دفعات خرید کمتر شود و در مواد اولیه وقتی مواد باکیفیت داشته باشیم، انرژی کمتری در فرایند تولید مصرف میشود و درعینحال مواد زائد کمتری تولید میگردد. همچنین نسوز کوره دیرتر خراب میشود. در اینجاست که میبینیم در پشت پرده کیفیت چه کاهش هزینهای وجود دارد. یکی دیگر از اصول سهگانه مربوط به زمان تدارک است. وقتی در زمان مناسب بتوانیم کالا و خدمات را فراهم کنیم، مثلاً هنگام توقف اضطراری یا تعمیرات برنامهریزیشده (شاتدانها) اگر نتوانیم قطعه موردنظر را فراهم کنیم، خط تولید با مشکل مواجه میشود یا شاید مجبور شویم از آن قطعه مستعمل دوباره استفاده کنیم و مجدداً خط متوقف شود که این امر هزینههای زیادی به بار میآورد. بخش بعدی قیمت مناسب است. وقتی بتوانیم با قیمت مناسبتری قطعات و مواد موردنیاز را تهیه کنیم، کاهش هزینهها مشهود خواهد بود. در زمینه بومیسازی در سال 1402 حدود 11.5 میلیون یورو صرفهجویی ارزی داشتهایم.
در حوزه بومیسازی فولاد مبارکه از پیشگامان مهندسی معکوس قطعات است، صرفهجوییهای اقتصادی تا چه حد به مهندسی معکوس و تولیدات خلاق داخلی مربوط است؟
بعد از اینکه مهندسی معکوس کار خود را شروع کرد، تمام قطعاتی که از خارج خریداری میشد تبدیل به نقشه گردید. در ابتدا نقشههای اطلاعاتی تهیه و بعد از ساخت و تأیید قطعات، وارد سیستم فولاد مبارکه شد. 90 تا 95 درصد از کل قطعات مکانیکی مورد استفاده در فولاد مبارکه در داخل کشور ساخته میشود. سال گذشته 88 درصد این قطعات ساخت داخل بود و به این میزان صرفهجویی ارزی منجر شد.
نگاه مدیریت شرکت به بومیسازی چگونه است؟
در دوره اخیر، مدیریت ارشد شرکت برای سرعت بخشیدن به حوزه تکنولوژی بر دو بال سرمایهگذاری و خرید خطرپذیر تمرکز و سرمایهگذاری کرده است. این راهبرد به میزان قابلتوجهی توانسته برای فولاد مبارکه گرهگشا باشد. یکی از راهبردهای مدیریت عالی سازمان که به جهش بزرگی در کسب دانش فنی و بومیسازی منجر شد استفاده از شرکتهای دانشبنیان طی دو سال اخیر بوده است. بعد از قطعاتی که در داخل کشور قابل ساخت بودند، در رویکرد جدید به سمت بومیسازی قطعات دارای تکنولوژی بالا در حال حرکتیم. بنابراین باید شرکتهایی باشند که بر پایه دانش استوار شده باشند. به همین منظور با همراهی معاونت تکنولوژی شرکت، با شناسایی شرکتهای دانشبنیان، از آنها دعوت کردیم تا ضمن حمایت، آنها را با خود همراه کنیم.
در حال حاضر چه تعداد شرکت دانشبنیان با فولاد مبارکه همکاری دارند و این همکاری چه نتایجی به دنبال داشته است؟
الآن 700 شرکت با فولاد مبارکه همکاری میکنند. سال 1401 حدود 5000 میلیارد و سال 1402 حدود 11 هزار میلیارد تومان با شرکتهای دانشبنیان کار کردیم و آنها هم گامهای بسیار بزرگی را برداشتند. قطعات استراتژیکی با همکاری این شرکتها بومیسازی شد که اگر نمیشد، در شرایط تحریمهای ظالمانه قطعاً دچار مشکل میشدیم.
شرکتهای دانشبنیان داخلی چند درصد توانستهاند نیاز داخلی را تأمین کنند؟ چه میزان از این سرمایهگذاری 11 هزار میلیاردی به فولاد مبارکه بازگشته است؟
فولاد مبارکه در همه حوزهها بهویژه در زمینه بومیسازی به بلوغ سازمانی رسیده است و بالطبع کارکنان دفاتر فنی و قسمتهای مهندسی معکوس یا بومیسازی نیز به دانشی رسیدهاند که سهم پرداختی ریسک کمتری داشته باشد. بهعنوان مثال، قالبهای ریختهگری فولاد سبا یکی از مهمترین قطعات در حوزه بومیسازی بود. ازآنجاکه این قالبها با فولاد مذاب سروکار دارد، بومیسازی آنها بسیار حساس است و شامل موارد پیچیده مهندسی میشود؛ اما خوشبختانه با بومیسازی آنها این سختی پشت سر گذاشته شد. همچنین پودرهای قالب، ریفورمر پمپها و کمپرسورها و بسیاری از تجهیزات دیگر از جمله موارد بسیار استراتژیک بود که اگر با همکاری دانشگاهها و شرکتهای دانشبنیان بومیسازی نمیشدند، حتماً دچار مشکل میشدیم. میتوان گفت تابهحال 80 تا 85 درصد از این سرمایهگذاریها به شرکت برگشت شده است و جواب مثبت گرفتهایم.
یکی از شاخصههای بومیسازی به نظارت بر کیفیت عملکرد تأمینکنندگان برمیگردد. در این باره توضیح دهید.
بومیسازی امروز در فولاد مبارکه یک فرایند است؛ فرایندی که روزی برای خاموش نشدن خط تولید شروع شد، ولی حالا برای تنوع بخشیدن به محصولات شرکت و اوجگیری نسبت به رقبا به یک اصل تبدیل شده است. شرکت فولاد مبارکه در راه خودکفایی و بومیسازی تجهیزات تاکنون برنامههای قابلتوجهی اجرا کرده است. راهی که مقصدش اقتدار و سربلندی ایران اسلامی است. از جمله این برنامهها طراحی و ساخت پیشرفتهترین و حساسترین تجهیزات هیدرولیکی در صنایع فولاد و دیگر صنایع، بومیسازی کورههای حرارتی در بخش نورد سرد، صفحات مسی قالبهای ریختهگری مداوم، بومیسازی دانش افزایش ضخامت تختال ماشین 5 از 200 و 250 به 300 میلیمتر است. مهندسی و امکان بومیسازی برای رسیدن به طرح استراتژیک شرکت و همینطور تولید فولاد سبز نیازمند تسهیل در تولید فناوری و ایجاد نوآوری بوده؛ اقدامی که فولاد مبارکه با تقویت شرکتهای خدماترسان دانشبنیان آن را پیش برده است. موضوع خریدهای خطرپذیر از سالها قبل شروع شده و باعث شده چرخه تکنولوژی در فولاد مبارکه با سرعت بیشتری حرکت کند. بومیسازی بزرگراهی بسیار طولانی است که مراحل مختلفی دارد. امروزه فولاد مبارکه به مراحلی رسیده که قطعات با تکنولوژی بالا و فناوریهای پیشرفته را دنبال میکنیم. برای تحقق این هدف، فولاد مبارکه علاوه بر سرمایهگذاری و خرید خطرپذیر در طول فرایند بومیسازی با به اشتراکگذاری دانش، بازرسیهای دقیقی را هم اعمال میکند.
مشخصاً کنترل کیفی در این میان چه جایگاهی دارد؟
در فولاد مبارکه برای اطمینان از خرید قطعات بومیسازیشده و ارتقای شرکتهای سازنده دو رویه کنترل کیفی وجود دارد: یکی از طریق بازرسیهای حین ساخت و تست سرد است که از همان ابتدا که سازنده قطعه یا تجهیزی را بهعنوان دستور کار بومیسازی قبول میکند، تیم کنترل کیفی ساخت داخل همراه با کارشناسان بومیسازی، ایستگاههای بومیسازی یا ایستگاههای کنترل کیفی کالا را با سازنده تنظیم میکنند و برنامه مشخصی دارند. در حین فرایند ساخت نیز کارشناسان بومیسازی و کنترل کیفیت ساخت قطعات یدکی بازرسیهای حین ساخت را انجام میدهند و در پایان ساخت، قبل از اینکه حمل تجهیز انجام و تجهیز یا قطعه وارد فولاد مبارکه شود، در صورت نیاز تستهای سرد در محل کارگاه سازنده انجام میشود و بعد از آن مجوز حمل صادر میشود.
در این میان نقش اعتماد به شرکتهای سازنده و دانشبنیان را چگونه توصیف میکنید؟
اعتماد به شرکتهای سازنده و دانشبنیان داخلی ضمن بازرسی حین ساخت باعث شده 1150 قطعه و تجهیز بومیسازی و به بهرهبرداری در خطوط تولید برسد. روندی که در زمان بهرهبرداری هم ادامه پیدا میکند تا به ایجاد شرکتهای صاحب برند در تولید خطوط فولادسازی در ایران کمک کند. ازآنجاکه قطعه عمر مفیدی دارد و یک دوره گارانتی، خود بهرهبردار مشابه یک قطعه خارجی با این قطعه برخورد میکند و از لحاظ عملکرد آن را رصد میکند. اگر در حین دوران گارانتی دچار مشکل شد، موارد به بومیسازی منعکس میشود و سازنده موظف است در دوره گارانتی آن را رفع عیب کند تا نهایتاً به آن نتیجه مطلوبی که موردنظر بهرهبردار و متقاضی است برسد. برای حمایت از سازنده نیز سازمان تصمیمگیری کرده که چند خرید بعدی قطعه بهصورت انحصاری از همان سازنده صورت گیرد.
رویکردی که در بومیسازی وجود دارد چقدر به صاحب تکنولوژی شدن فولاد مبارکه کمک کرده تا برند شرکت را بهعنوان طراح، توسعهدهنده و راهاندازیکننده خطوط فولاد جا بیندازد؟
اگر ما کنترل کیفیت نداشتیم، اصلاً نمیتوانستیم سطح دانش سازندهها را افزایش دهیم. سازندگان و شرکتهای دانشبنیان در چنین حالتی است که ناچارند با زبان مهندسی و دانش صحبت کنند و با نرمافزارهای روز دنیا کار کنند. این بازرسیها باعث شده شرکتها سطح دانش خود را بالا ببرند. اگر بازرسیهای مستمر و دقیق نباشد، زمانی که قطعه ساختهشده نصب شد، قطعاً مشکلات عدیدهای را به همراه خواهد آورد.
در این حوزهها با چه چالشهایی مواجهید؟
با توجه به اینکه تحریمهای ظالمانه وجود دارد، خود ما باید درصدد باشیم برای خودمان مانع درست نکنیم. یکی از موانعی که انتظار داریم وزارت صمت پیگیر رفع آن باشد موضوعات مربوط به گمرک و تخصیص ارز و ثبت سفارش است که زمان اینها طولانی شده و باعث میشود زمان تدارک قطعات افزایش یابد. چالش دیگر در خصوص مواد اولیه است و ما نباید خامفروشی داشته باشیم. خامفروشی باعث به هم خوردن عرضه و تقاضا میشود و قیمت مواد اولیه را برای تولیدکنندگان داخلی بالا میبرد. متأسفانه امروز شرکتهای معدنی بهنوعی خودشان فولادساز شدهاند و مواد اولیه تولیدی را خودشان استفاده میکنند و این باعث میشود ما برای تولید پایدار بهناچار به دنبال معادن باشیم.
یکی از چالشهای مهم در زمینه ساخت قطعات این است که سازندهها در ساخت بعضی از قطعات دچار محدودیت هستند و حتی از تعداد انگشتهای یک دست هم کمتر تولید میکنند. ما باید بتوانیم سرمایهگذاری کنیم و با شرکتهای زیرمجموعه مشارکتی را با شرکتهای توانمند و سازنده ایجاد کنیم تا بتوانیم تعداد ساخت قطعات مهم و استراتژیک را اضافه کنیم.
آیا با توان فعلی در حوزه بومیسازی، شرکت میتواند امیدوار باشد بنابر سفارش، خط ریختهگری طراحی و اجرا کند؟
در خط ریختهگری ما بیشتر قطعات را در داخل میسازیم. البته نهتنها در خط ریختهگری، بلکه در نورد گرم و در فولادسازی هم همین شرایط حاکم شده است. برای اینکه تمام خط را بسازیم مشکلی نداریم؛ اما بحث مهندسی برنامهریزی و فرایندها وجود دارد که انتظار میرود قسمت فنی و مهندسی ما که به همین منظور تشکیل شدهاند، بتوانند تکنولوژیهای روز دنیا را به دست آورند و ما بتوانیم در ایجاد خطوط بعدی از صفر تا صد عمل کنیم. از نظر ساخت قطعات واقعاً مشکلی نداریم و در توسعهها هم میبینیم بیشتر قطعات را میتوانیم بومیسازی کنیم. آنچه باقی میماند بحث نرمافزاری و فرایندی است که قسمت فنی و مهندسی باید در این زمینه گامهای بلندتری بردارد.
فولاد مبارکه با توجه به نیازهای خود و فولادسازان داخلی بیشتر در کدام حوزه باید برای تحقق برند کار کند؟
برندسازی باید از پایه و از خود کارکنان شروع شود تا به برندسازی کلیه قطعات و کارخانه منجر شود. دستیابی به دانش روز دنیا در ساخت قطعات و خط تولید یا توانایی تولید نسوز کل کوره یا قالب ریختهگری که یکی از قطعات بسیار مهم است بهطورکلی به برندسازی منتهی میشود. وقتی خود کارکنان با همت و تلاش و دانش جلو میروند و از سویی، در قطعات و تجهیزات و دیگر قسمتها ساخت داخل انجام میشود، درمجموع برندسازی بسیار خوبی صورت میگیرد. در این حالت شرکتهای دیگری که بخواهند از اینها استفاده کنند میبینند جرقه اول در فولاد مبارکه زده شده است.
سخن آخر؟
برای پیروزی بر بدخواهان کشور کافی است افراد توانمند آستین همت بالا بزنند و به میدان عمل بیایند. فولاد مبارکه مولود انقلاب است و کارکنان پرتلاش و دلسوزی از بدو امر تا امروز در این شرکت فعالیت کردهاند. حتماً میتوانیم پازل صنعتی را که دست ما است با تصویر زیباتری کامل کنیم.